Standard hydraulic fittings and hoses often fall short when faced with demanding applications. Off-the-shelf components may not withstand extreme pressures, temperatures, or aggressive media, leading to inefficiency and potential failure. For industries requiring tailored solutions, especially under special operating conditions or for large volume production, custom hydraulic fittings and non-standard hose assemblies become essential. These bespoke solutions offer enhanced performance, reliability, and safety, ensuring your hydraulic systems operate flawlessly even in the most challenging environments. This article explores how custom solutions meet these unique demands, driving efficiency and dependability.
The Limitations of Standard Hydraulic Components: Recognizing the Need for Customization
While standardized hydraulic components offer interchangeability and cost-efficiency for many applications, their inherent design compromises become critical liabilities when pushed beyond conventional boundaries. Relying on standard parts in demanding scenarios involving extreme temperatures, high pressures, aggressive chemicals, tight spaces, or significant vibration often leads to suboptimal performance and significant hidden costs. Component failures cause unscheduled downtime, directly impacting revenue and operational efficiency. Frequent replacements drive up maintenance labor and inventory expenses. Most critically, failures in hydraulic systems pose serious safety risks, including high-pressure fluid injection injuries, loss of equipment control, and fire hazards. Furthermore, inadequate connections contribute to energy loss and reduced system efficiency. Recognizing these limitations and the associated costs—downtime, maintenance, safety risks, and inefficiency—underscores the compelling value proposition of investing in custom hydraulic solutions engineered specifically for your unique application demands.
Defining Custom Hydraulic Fittings and Non-Standard Hose Assemblies: Engineered for Purpose
When standard components are inadequate, custom hydraulic fittings and non-standard hose assemblies provide the necessary solution. These are not mere variations but components specifically engineered to meet precise requirements outside standard offerings.
What Makes a Fitting ‘Custom’?
Customization addresses specific challenges where standard fittings fail:
- Unique Geometries & Dimensions: Tailored shapes, non-standard lengths, specific bend radii, or reduced/enlarged hex sizes to fit confined spaces or integrate seamlessly. This includes multi-port manifolds consolidating connections.
- Non-Standard Threads & Ports: Interfacing with legacy equipment, less common standards, or proprietary designs often requires unusual thread pitches, diameters, or sealing methods.
- Integrated Features: Incorporating check valves, orifices, test points, sensor ports, or special mounting features directly into the fitting simplifies system design and reduces potential leak paths.
- Specialized Materials: Moving beyond standard steel or brass to materials chosen for specific properties: various stainless steel grades (316L, Duplex), high-strength alloys, titanium, Monel, Hastelloy, or engineered plastics (PEEK, PTFE) for extreme pressure, corrosion resistance, weight savings, or chemical inertness.
- Enhanced Performance Ratings: Engineering components to exceed standard pressure, temperature, or vibration resistance limits through material choice, modified design (e.g., increased wall thickness), and rigorous validation testing.
- Specific Coatings: Applying specialized coatings (e.g., zinc-nickel, electroless nickel) for enhanced corrosion protection, wear resistance, or regulatory compliance.
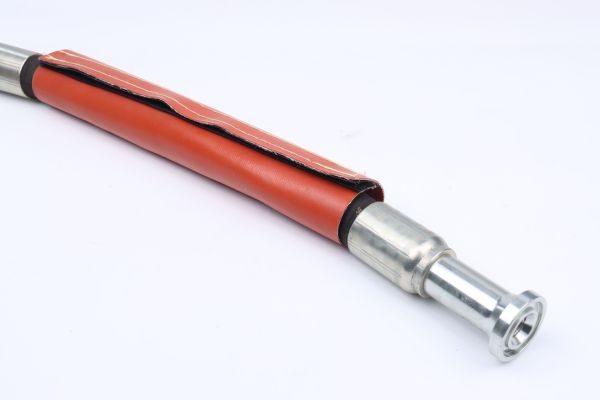
Understanding Non-Standard Hose Assemblies
A non-standard hose assembly involves tailoring the hose, the fittings, or the assembly method for demanding requirements:
Hoses for Specific Challenges: Engineered to overcome:
- Extreme Temperatures: Using materials like silicone, PTFE, or specialized synthetics for high heat or cryogenic conditions.
- Aggressive Chemicals: Employing tube materials like PTFE, nylon, or specific elastomers resistant to the conveyed media.
- Ultra-High Pressure (UHP): Constructed with multiple high-tensile steel wire spiral layers for applications like water jetting.
- Flexibility/Bend Radius: Achieving greater flexibility or a smaller bend radius for tight routing.
- Abrasion Resistance: Utilizing highly durable cover materials (e.g., UHMWPE) or protective sleeving.
- Other Needs: Electrical non-conductivity, specific colors, low permeation, or compliance with food/pharmaceutical standards.
Specialized Construction: Involves careful selection of the inner tube, reinforcement layers (type and number), and outer cover to meet pressure, temperature, flexibility, and environmental requirements.
The Assembly is Key: Ensuring compatibility between the non-standard hose and appropriate fittings (often custom themselves) and using precise, manufacturer-specified crimping/attachment processes are critical for a reliable, leak-proof connection capable of withstanding the full operating conditions.
Understanding these custom characteristics allows for the specification of solutions truly optimized for performance and reliability.
Mastering Special Operating Conditions with Custom Solutions
Custom hydraulic components excel where standard parts fail, particularly under extreme conditions. Leveraging advanced materials and tailored designs ensures reliability and performance in challenging environments.
Tackling Extreme Pressures (UHP)
Ultra-high pressure (UHP) systems (>700 bar / 10,000 psi) in applications like waterjet cutting or hydrostatic testing demand specialized components.
- Materials: High-strength alloy steels or specialized stainless grades are necessary, considering fatigue life under cyclic loading.
- Design: Increased wall thickness, specialized thread forms (e.g., cone-and-thread), and robust sealing mechanisms (metal-to-metal or specialized polymers) are crucial.
- Hoses: UHP hoses require multiple (often 6+) high-tensile steel spiral layers, robust materials, and specialized UHP fittings with precise assembly.
Conquering Temperature Extremes
Operating significantly outside the standard -40°C to +100°C range requires careful material selection.
- High Temperatures: Use fittings made from stainless steel grades (316, 321) or nickel alloys (Inconel). Employ high-temperature seals (FKM, FFKM, Silicone, PTFE) and hoses with temperature-resistant tubes/covers (silicone, PTFE).
- Low Temperatures: Select fitting materials (specific stainless grades) that maintain ductility. Use specialized low-temperature elastomers or PTFE seals and hoses designed for flexibility in cold environments.
- Design: Consider thermal expansion/contraction to maintain seal integrity across the temperature range.
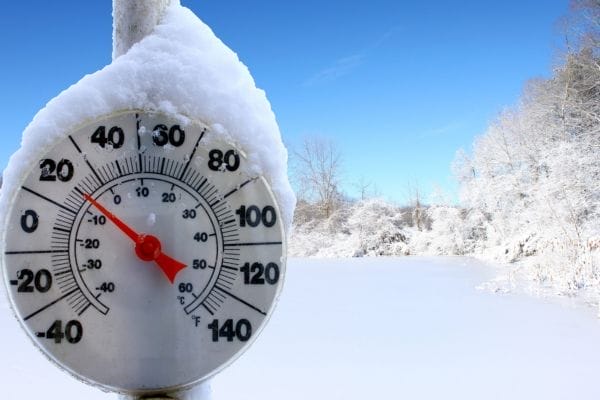
Ensuring Compatibility with Aggressive Media
Chemicals, solvents, or saltwater can corrode standard materials and degrade seals.
- Materials: Custom fittings may use 316L, Duplex/Super Duplex stainless steel, Monel, Hastelloy, Titanium, or PTFE linings for superior corrosion resistance.
- Seals: Select elastomers (FKM, FFKM, EPDM, PTFE) based on detailed chemical compatibility charts for the specific fluid, temperature, and pressure.
- Validation: Testing under simulated or actual conditions is often necessary to confirm long-term compatibility.
Surviving High Vibration and Dynamic Loads
Vibration can cause fatigue failure and loosen standard threaded connections.
- Fitting Designs: Utilize vibration-resistant designs like O-Ring Face Seal (ORFS – SAE J1453), properly supported flare fittings, or specialized locking mechanisms. Select materials with high fatigue strength.
- Hose Assemblies: Ensure proper routing, use clamps/supports, and select hoses with high impulse life ratings tested under dynamic pressure cycles.
Addressing Unique Environmental Challenges
- Abrasion: Use hoses with highly abrasion-resistant covers (UHMWPE) or protective sleeving (nylon, spring guards).
- UV/Ozone: Employ hoses with cover materials specifically formulated for UV and ozone resistance in outdoor applications.
- Corrosion: For subsea or marine environments, use fittings made from Super Duplex, Titanium, or Monel, often with protective coatings.
By addressing these conditions through tailored design and materials, custom solutions deliver essential performance and reliability.
Meeting the Demands of Large Volume Production: Consistency at Scale
OEMs and large industrial users often require customized hydraulic solutions produced in high volumes, necessitating unwavering consistency, reliability, scalability, and cost-effectiveness.
The OEM Challenge: Balancing Customization with Scale
OEMs require custom hydraulic components that deliver optimal performance and perfect fit for their specific equipment designs. However, they also face the challenge of ensuring:
- Consistency: Each unit must match the quality and performance of the first, ensuring uniformity across thousands of units.
- Reliability: Absolute dependability is essential to protect the OEM’s brand reputation.
- Scalability: The ability to adjust production to meet fluctuating demands, often requiring Just-In-Time (JIT) solutions.
- Cost Management: OEMs need to balance initial design costs with total cost of ownership (TCO) to keep production efficient and affordable.
Topa’s Manufacturing Capabilities for High-Volume Customization
To produce custom parts at scale, Topa invests in cutting-edge technologies and optimized production methods:
- Advanced Machining: Utilizing high-speed CNC lathes, multi-spindle machines, and automated cells to ensure precision at high volumes.
- Automation: Incorporating robotics for machine tending, inspection, and material handling to streamline operations, increase throughput, and minimize variability.
- Efficient Tooling: Implementing robust tooling designs and management systems to handle high-volume runs with precision.
- Automated Assembly: Automated processes like hose cutting, fitting insertion, and crimping ensure consistency in hose assemblies.
Ensuring Quality Control at Scale
To guarantee top-tier quality across large-scale production runs, Topa implements a rigorous quality control system:
- Robust QMS: An effective Quality Management System, such as ISO 9001, ensures consistent adherence to global quality standards.
- Statistical Process Control (SPC): Real-time monitoring of critical dimensions and parameters helps detect and prevent production deviations.
- Automated Inspection: Vision systems, CMMs (Coordinate Measuring Machines), and automated gauging are used for high-frequency or 100% inspection, ensuring every part meets exact specifications.
- Rigorous Testing: Pressure, leak, material verification, and dimensional checks are consistently applied to confirm product integrity.
- Lot Traceability: Complete traceability from raw material to finished product enables detailed root cause analysis and effective recall management if needed.
Achieving Cost-Effectiveness in Volume
Custom parts can be cost-effective at high volumes when using the right strategies:
- Economies of Scale: Bulk material purchasing and optimized machine utilization lead to reduced per-piece costs.
- Process Optimization: Applying lean manufacturing principles to eliminate waste and improve overall efficiency.
- Design for Manufacturability (DFM): Early collaboration between the customer and Topa’s engineering team ensures that designs are optimized for cost-effective production.
- Focus on TCO: By prioritizing improved reliability, extended product life, and reduced warranty costs, Topa helps OEMs achieve lower total ownership costs in the long run.
Topa’s advanced manufacturing processes and strict quality control measures ensure that we consistently deliver custom hydraulic solutions that are reliable, scalable, and cost-effective—helping OEMs meet their large-volume demands with precision.
The Customization Journey: A Collaborative Path to Precision
Developing a custom hydraulic solution requires a structured, collaborative process to ensure the final product meets the exact needs of the OEM.
Step 1: Consultation and Requirement Definition
In this critical phase, we engage in detailed discussions with the customer to fully understand the application, define operating conditions (pressure, temperature, flow, media, environment), and identify specific performance goals. Additionally, we establish volume and timeline requirements. This phase relies on open communication between the customer’s application experts and Topa’s engineering team.
Step 2: Design and Engineering
We transform the requirements into a comprehensive design using advanced CAD modeling, incorporating FEA (Finite Element Analysis) or CFD (Computational Fluid Dynamics) simulations for detailed analysis. Our engineering team selects optimal materials for all components, including fittings, seals, and hoses, and designs custom seal configurations. We also create detailed manufacturing drawings with precise tolerances and specifications to guide production.
Step 3: Prototyping and Validation
After the design phase, we produce initial prototypes for customer evaluation. These samples undergo rigorous testing to ensure they meet fit, function, and performance standards. Tests include dimensional checks, pressure/leak tests, temperature cycling, impulse tests, and material verification. The customer’s approval of validated prototypes is crucial before proceeding to full-scale production.
Step 4: Scaling to Full Production
Once the prototype is approved, we finalize production tooling, schedule manufacturing based on forecasts, and implement quality control procedures. Topa’s automated systems ensure consistent production based on approved designs. We also manage logistics to ensure on-time delivery, guaranteeing that each batch meets the defined specifications and quality standards.
This structured, collaborative approach ensures that the final custom hydraulic components not only meet but exceed the required performance and quality expectations.
Conclusion
Standard hydraulic components reach their limits when faced with special operating conditions or the rigorous demands of large volume production. Custom hydraulic fittings and non-standard hose assemblies provide the essential solution, delivering tailored performance, enhanced reliability, and optimal integration. By partnering with a specialist provider, you gain access to deep engineering expertise and advanced manufacturing capabilities. Don’t compromise on performance or safety. Contact us today to discuss your unique hydraulic connection challenges and let our experts engineer the perfect custom solution for your specific needs.
FAQ
What are custom hydraulic hose fittings?
Custom hydraulic hose fittings are specifically designed to meet unique application requirements. They are tailored to fit particular sizes, materials, and pressure specifications, ensuring optimal performance in a specific hydraulic system.
Why should I choose custom hydraulic hose fittings over standard ones?
Custom fittings provide a better fit for your hydraulic system, offering improved sealing, performance, and durability. They can also be designed to handle specific pressure, temperature, and environmental conditions that standard fittings may not accommodate.
How do I determine the right custom hydraulic hose fitting for my needs?
The right fitting depends on your system’s specifications, including pressure, flow, temperature, and the type of fluid being used. Consulting with an experienced supplier or engineer can help ensure the proper selection of fittings based on your unique application.
What materials are typically used for custom hydraulic hose fittings?
Common materials include stainless steel, carbon steel, brass, and alloy steel. The material choice depends on factors like corrosion resistance, pressure requirements, and the environment in which the hose fitting will be used.
How long does it take to produce custom hydraulic hose fittings?
The production timeline for custom fittings can vary depending on the complexity of the design, material selection, and manufacturing process. On average, it may take a few weeks from consultation to delivery, but expedited services can be arranged for urgent orders.
How do I ensure the quality of custom hydraulic hose fittings?
Ensure quality by choosing a supplier with a robust Quality Management System (QMS) like ISO 9001 certification. Additionally, request detailed testing for pressure, leak, and material verification to confirm the fittings meet the required specifications for your system.