Sealing is a vital aspect of hydraulic systems as it prevents leaks, maintains the system’s pressure integrity, and ensures the safe and efficient operation of the entire setup. Without proper sealing, hydraulic systems can experience performance degradation, loss of power, or even complete failure.
What is Hydraulic Fitting Sealing?
Hydraulic systems are widely used across a variety of industries for their ability to transmit power and perform work efficiently. These systems rely on the precise flow of pressurized fluid to move machinery and perform tasks such as lifting, pressing, and driving mechanical processes.
Sealing in hydraulic fittings refers to the process of ensuring that fluid within the system remains contained at the connection points of pipes, hoses, valves, and other components. In a hydraulic system, fittings are used to connect various parts of the fluid circuit, and each of these connections must be properly sealed to prevent fluid leakage. A hydraulic fitting seal provides a barrier that stops fluid from escaping, which could compromise system performance, cause power loss, or even lead to hazardous conditions.
In essence, hydraulic fitting seals are designed to keep the hydraulic fluid at its optimal pressure, preventing leaks that could undermine the efficiency and safety of the system. In a hydraulic system, where fluids are generally under high pressure, these seals must not only prevent leakage but also withstand the extreme conditions of the system, including high pressures, variable temperatures, and potential chemical exposure.
Types of Seal Materials in Hydraulic Fittings
The selection of appropriate sealing material is paramount in maintaining the integrity of the hydraulic system. The right material must be chosen based on various factors, such as system pressure, temperature, fluid type, and the specific demands of the application. The most commonly used seal materials for hydraulic fittings are:
1. Rubber Seals
Rubber seals are one of the most common types of seals used in hydraulic fittings, thanks to their excellent flexibility, cost-effectiveness, and compatibility with various hydraulic fluids. The most commonly used rubber materials for hydraulic seals include Nitrile (Buna-N), EPDM (Ethylene Propylene Diene Monomer), and Neoprene. These materials provide excellent sealing in low to medium-pressure applications and are effective at sealing against a wide range of fluids such as water, oil, and grease.
2. Metal Seals
Metal seals are used in environments where rubber or elastomeric seals may not be able to perform effectively due to high pressure or extreme temperatures. Metal-to-metal sealing is commonly used in high-pressure applications such as power plants, offshore rigs, and aerospace applications. Metal seals are constructed from materials such as stainless steel, brass, or titanium, which provide excellent durability and resistance to wear.
3. Elastomeric Seals
Elastomeric seals are typically made from synthetic rubbers like Viton, Silicone, and Fluorosilicone. These materials are known for their ability to handle higher temperatures, aggressive chemicals, and harsh hydraulic fluids.
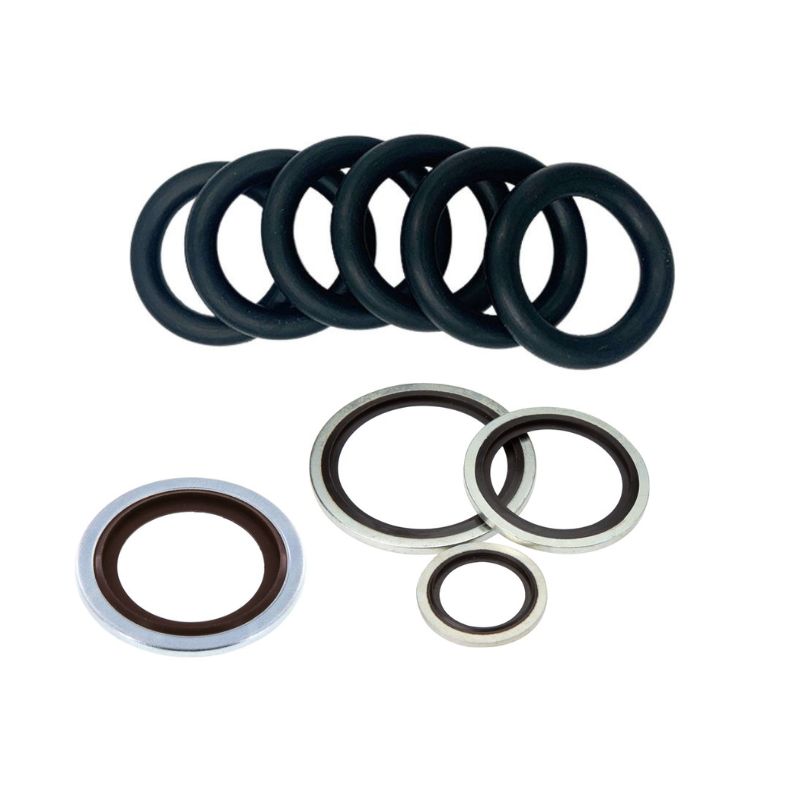
Purpose of Hydraulic Fitting Seals
The primary purposes of hydraulic fitting seals are as follows:
Prevent Leaks: Hydraulic systems operate under high pressure, and even a small leak can result in significant fluid loss, reduced system performance, and even catastrophic failure. Seals prevent the fluid from escaping at the connection points of pipes, hoses, valves, and other hydraulic components, thereby maintaining the integrity of the system. Leak prevention also reduces the environmental impact of hydraulic fluid loss.
Protect Against Contamination: Contaminants, such as dirt, water, air, and debris, can damage the hydraulic fluid and components, leading to reduced efficiency and failure of the system. Hydraulic fitting seals protect the fluid from contamination by preventing foreign particles from entering the system. This helps ensure that the hydraulic fluid remains clean and maintains its operational properties, thus enhancing the performance and longevity of the system.
Maintain Pressure Integrity: Hydraulic systems rely on the precise control of pressure to perform tasks effectively. Seals help maintain this pressure by preventing leaks that would otherwise cause fluctuations in system pressure. Maintaining stable pressure is essential for the efficient operation of the system, as even minor pressure drops can lead to inefficiency, poor performance, or system failure.
Types of Hydraulic Fitting Seals
O-Ring Seals
O-ring seals are one of the most common and versatile sealing solutions used in hydraulic fittings. An O-ring consists of a simple circular elastomeric ring designed to fit into a groove on the mating surface of two parts. When compressed between the surfaces, the O-ring creates a tight seal, preventing fluid leakage.
Advantages:
Cost-effective: O-rings are relatively inexpensive to produce and easy to install, making them a popular choice for many applications.
Versatility: They are suitable for a wide range of pressure levels and are compatible with most fluids, including oils, water, and gases.
Simple Design: The design of O-rings is straightforward, reducing the system’s complexity and the likelihood of installation errors.
Disadvantages:
Limited High-Temperature Tolerance: O-rings can degrade under extreme temperatures, especially in high-heat applications unless made from specialized materials.
Compression Set: Over time, O-rings can lose their elasticity and become prone to leaks, particularly if the system is exposed to high pressures or fluctuating temperatures.
Common Applications: O-ring seals are used extensively in hydraulic cylinders, valve assemblies, pumps, and hose connections. Their ability to seal both static and dynamic connections makes them invaluable in systems with regular movement or vibration.
Installation Tips:
Ensure the groove dimensions are correct to prevent the O-ring from being over-compressed or pinched.
Lubricate the O-ring before installation to avoid damage during fitting.
Inspect the O-ring for cracks or defects before use to prevent leaks.
Compression Seals
Compression seals work by forming a seal through the application of pressure between the mating surfaces of two parts. These seals are typically made from elastomeric materials like rubber or silicone, and they rely on compressive force to create a barrier against fluid leakage.
Benefits:
Effective under Pressure: Compression seals are effective in high-pressure applications, providing a strong barrier between components.
Simple Design: These seals are easy to install and replace, making maintenance straightforward.
Flexibility: Compression seals can accommodate slight variations in the surface or alignment of parts.
Limitations:
Limited Durability: Over time, compression seals can lose their elasticity, which may lead to leaks if not properly maintained or replaced.
Deformation: Continuous compression may lead to the deformation of the seal, affecting its ability to maintain a tight seal.
Typical Applications: Compression seals are commonly used in hydraulic systems with fixed joints, such as flanged fittings, pipe connections, and valves. Their ability to maintain a seal under static pressure makes them ideal for these applications.
Flanged Seals
Flanged seals consist of a metal or elastomeric sealing ring that fits into a flange groove, providing a tight seal when the two flanged components are bolted together. This type of seal is often used in high-pressure and high-temperature environments.
How They Work: The flanged seal works by using the flange’s pressure to compress the seal, creating a barrier against leakage. The seal’s material properties allow it to deform slightly to ensure a snug fit between the parts.
Pros:
High-Pressure Resistance: Flanged seals can withstand extremely high pressures without failure, making them ideal for heavy-duty hydraulic systems.
Durability: These seals are typically durable and have a long service life.
Reliable Seal: Flanged seals are highly reliable and are less prone to failure due to their robust construction.
Cons:
Installation Complexity: Installation can be more involved than simpler seals, requiring careful alignment and bolts or fasteners.
Cost: Flanged seals tend to be more expensive than basic seals, both in terms of material costs and installation.
Common Applications: Flanged seals are commonly found in large hydraulic systems, such as those used in heavy machinery, power plants, and offshore oil rigs. They are also used in heat exchangers and other high-pressure applications.
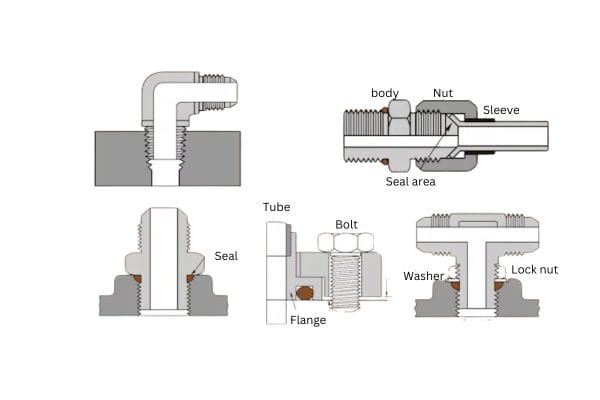
Threaded Seals
Threaded seals are used in fittings that involve threaded connections, where a sealant is applied to the threads to prevent fluid leaks. These seals can be created using various materials such as Teflon tape, anaerobic sealants, or metal-based compounds.
How They Work: The sealing material fills the gaps between the threads when the connection is tightened, forming a seal that prevents fluid from escaping. The compressive forces from tightening the threaded parts also help in forming a stronger seal.
When to Use: Threaded seals are typically used in applications where components are joined by threaded connections. They are especially useful when disassembly is needed for maintenance or repair.
Benefits:
Ease of Use: Threaded seals are relatively easy to apply, especially with pre-applied sealants.
Adaptability: They can be used in a variety of sizes and configurations.
Leak Prevention: They provide an excellent seal against both fluids and gases, preventing leakage from the threads.
Challenges:
Installation Care: Over-tightening or under-tightening threaded seals can cause leaks or damage to the components.
Material Compatibility: Some sealants may degrade with exposure to certain hydraulic fluids, limiting their use in specific environments.
Metal-to-Metal Seals
Metal-to-metal seals are used in high-pressure and high-temperature applications where elastomeric seals may not perform adequately. These seals consist of metal components that form a tight seal without the use of elastomeric materials. The metal sealing surfaces create a barrier by being compressed against one another.
How They Function: In metal-to-metal seals, the mating surfaces of the two parts are designed to be smooth and perfectly aligned. When pressure is applied, the metal surfaces deform slightly, creating a seal that is resistant to leakage.
Advantages:
Extreme Durability: Metal-to-metal seals are extremely durable and can withstand extreme conditions without failing, making them ideal for harsh environments.
High-Temperature and Pressure Resistance: They are particularly useful in systems that operate under very high pressures and temperatures, where traditional sealing materials might fail.
Longevity: These seals have a longer service life compared to elastomeric seals in certain applications, especially in aggressive environments.
Factors to Consider When Choosing Hydraulic Fitting Sealing Methods
Selecting the right sealing method for hydraulic fittings is crucial for the performance, efficiency, and safety of a hydraulic system. Several factors influence the decision-making process, including the system’s pressure and temperature, the type of hydraulic fluid used, and the environmental conditions in which the system operates.
Pressure and Temperature
Pressure and temperature are two of the most critical factors that affect the selection of sealing materials for hydraulic systems. The sealing material must be capable of withstanding the operating pressures and temperatures without failing, degrading, or losing its sealing ability.
Pressure: Seals must maintain their integrity even under varying levels of pressure. High-pressure systems, such as those used in heavy machinery, power generation, and oil rigs, require seals that can withstand significant stress without failure. Materials like metal seals and high-performance elastomers (e.g., Viton or HNBR) are suitable for such applications. For lower-pressure systems, seals made of rubber (e.g., Nitrile) are often sufficient.
Temperature: Extreme temperatures can cause materials to degrade, harden, or become too soft, leading to loss of sealing ability. For high-temperature applications (above 200°F / 93°C), Viton seals are preferred due to their high-temperature resistance. In contrast, systems that operate at lower temperatures may use materials like EPDM or Nitrile, which are more cost-effective and perform well within moderate temperature ranges. Choosing the correct material ensures that the seal remains effective and doesn’t break down under thermal stress.
For both temperature and pressure extremes, metal-to-metal seals or high-performance elastomers are ideal as they can handle the stresses of both high pressures and temperatures.
Fluid Compatibility
The type of hydraulic fluid used in the system plays a significant role in choosing the right seal material. Hydraulic fluids can vary widely in terms of their chemical properties, including oil-based, water-based, synthetic fluids, and more. Each of these fluids interacts differently with seal materials, which is why compatibility must be carefully considered.
Chemical Resistance: Certain hydraulic fluids, such as phosphate esters or synthetic oils, may react adversely with some seal materials, leading to degradation, swelling, or hardening of the seal. For example, Nitrile rubber is highly compatible with mineral oils but may degrade in contact with water-based fluids. On the other hand, Viton or fluoro silicone seals are more chemically resistant and are better suited for aggressive fluids or environments where fluid types may change.
Hydraulic Fluid Type: Oil-based hydraulic fluids often work well with Nitrile (Buna-N) seals, while water-based fluids such as water-glycol or phosphate ester fluids require materials with higher chemical resistance, such as EPDM or Viton. For systems using synthetic fluids or fuels, seals made from materials like Fluorosilicone or PTFE are often recommended.
Selecting the correct seal material based on the fluid type helps prevent chemical degradation, ensuring the system’s longevity and reliability.
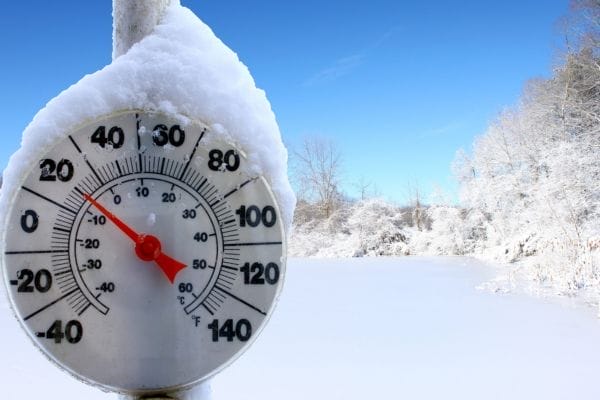
Environmental Considerations
Environmental factors can have a significant impact on the performance and lifespan of hydraulic seals. Exposure to elements such as water, dust, ultraviolet (UV) rays, and chemicals in the atmosphere can degrade seals over time. Choosing seals that can withstand these environmental factors is essential for maintaining system integrity.
Water Exposure: In environments where seals are exposed to moisture or water, materials like EPDM and Nitrile offer resistance to water absorption and maintain their sealing properties even when exposed to wet conditions. Fluorosilicone seals are also highly resistant to water and can perform well in marine environments or where frequent washdowns are necessary.
Dust and Debris: Seals used in dusty or dirty environments, such as construction or mining, must be resistant to abrasion and capable of preventing particles from entering the system. Rubber seals (e.g., Nitrile) or elastomers like HNBR are suitable for these environments as they can form tight seals that prevent dirt and debris from contaminating the hydraulic fluid.
UV Exposure: For outdoor hydraulic systems exposed to sunlight, UV-resistant materials like EPDM and Silicone seals are recommended. UV rays can cause degradation in standard rubber materials, leading to hardening, cracking, and loss of sealing capability.
Common Issues with Hydraulic Fitting Seals and How to Prevent Them
Leaking Seals
One of the most prevalent issues with hydraulic seals is leakage, often caused by improper installation, misalignment, or wear. Over time, seals can degrade, leading to small gaps that allow fluid to escape.
Causes: Leaking seals may result from insufficient compression, incorrect sizing, damage during installation, or wear due to high-pressure cycles. Misalignment of components or improper assembly can also lead to leaks.
Prevention Tips:
Ensure that seals are the correct size and fit snugly within their grooves.
Use lubrication during installation to prevent tearing and to allow seals to settle correctly.
Regularly inspect seals for signs of wear or damage and replace them as needed.
Align components carefully to avoid creating uneven pressure on the seals, which can lead to leaks over time.
Wear and Tear on Seals
Common Causes of Seal Degradation: Seals in hydraulic systems are subjected to constant friction, pressure, and sometimes harsh chemicals. Over time, this exposure can lead to degradation, reducing the seal’s ability to function effectively. Common causes of wear and tear on seals include:
Abrasion: Friction between the seal and the mating surfaces can cause the material to wear down, leading to leaks. In high-velocity systems, abrasion can be accelerated.
Over-Compression: When seals are compressed beyond their design limits, they may lose their shape or become permanently deformed, leading to ineffective sealing and eventual failure.
Chemical Exposure: Harsh fluids or chemicals can degrade certain seal materials, leading to cracking or swelling, which compromises the seal.
Best Practices to Prevent Premature Wear
To minimize wear and tear on seals, the following measures should be taken:
Use Appropriate Materials: Select seal materials that are suited to the specific operating conditions of the system. For example, choose seals made of high-resilience materials for high-friction environments or elastomers with better chemical resistance when dealing with aggressive fluids.
Regular Inspection and Cleaning: Inspect seals regularly for signs of wear or damage, such as cracks, abrasions, or swelling. Cleaning the seals to remove dirt or debris can also help prevent abrasion.
Ensure Correct Fit: Properly hydraulic fitting seals are less likely to experience over-compression or uneven wear. Ensure that the seal dimensions match the fitting precisely to avoid excess pressure on the seal.
Seal Material Failure
Reasons for Seal Material Failure: Seal material failure can occur when the seal material no longer performs as intended, which can be due to several factors:
Temperature Extremes: Exposure to temperatures outside the recommended range for the seal material can cause it to harden, soften, or degrade, leading to failure. For example, rubber seals may become brittle at low temperatures, while elastomers may soften or swell at high temperatures.
Fluid Compatibility Issues: If the seal material is not compatible with the hydraulic fluid, it can degrade or swell, leading to failure. For instance, Nitrile seals are not suitable for systems using phosphate ester-based fluids, as they degrade rapidly.
UV and Environmental Damage: UV exposure, especially in outdoor applications, can cause certain seal materials to crack or become brittle over time. Similarly, exposure to dust, dirt, or water can impact seal performance.
How to Select the Right Materials to Prevent Failures
To minimize the risk of seal material failure, the following steps should be taken:
Temperature and Fluid Compatibility: Ensure that the selected seal material is designed to withstand the operating temperature and is compatible with the type of hydraulic fluid in use. For instance, Viton is suitable for high-temperature applications, while EPDM is ideal for water-based fluids.
Environmental Protection: If the seal is exposed to harsh environmental conditions, choose materials with UV resistance or the ability to withstand abrasion. Silicone and HNBR (Hydrogenated Nitrile Butadiene Rubber) are good choices for UV-resilient applications.
Conclusion
The right seal material not only prolongs the life of the system and its components but also improves overall system performance and minimizes downtime and costly repairs. Investing in high-quality seals tailored to your system’s needs is a crucial step in maintaining smooth operation and ensuring safety in demanding environments.
FAQ
What is the purpose of hydraulic fitting seals?
Hydraulic fitting seals are designed to prevent fluid leaks, protect against contamination, and maintain pressure integrity in hydraulic systems. They ensure the system operates efficiently and safely by keeping the fluid contained within the components.
What materials are commonly used for hydraulic seals?
Common seal materials include rubber (e.g., Nitrile, EPDM), elastomers (e.g., Viton, Fluorosilicone), and metal (e.g., stainless steel, brass). The choice of material depends on the system’s pressure, temperature, and fluid compatibility.
How do temperature and pressure affect seal performance?
Extreme temperatures and high pressures can cause seals to degrade or lose their sealing capabilities. It’s crucial to select materials that can withstand the system’s operating conditions. For high-temperature or high-pressure systems, materials like Viton or metal seals are often used.
What factors should I consider when selecting a hydraulic seal?
Key factors include the system’s pressure and temperature, the type of hydraulic fluid used, and environmental conditions (e.g., exposure to water, dust, UV rays). These factors determine the most suitable seal material for your system.
How often should hydraulic seals be replaced?
Hydraulic seals should be inspected regularly for wear and tear. The replacement frequency depends on system usage, fluid conditions, and environmental factors. If seals begin to leak or show signs of degradation, they should be replaced immediately to prevent system failure.
Can a single type of seal be used for all hydraulic systems?
No, each hydraulic system has specific requirements based on pressure, temperature, and fluid type. It’s important to choose the right seal type tailored to the particular conditions of your system for optimal performance and longevity.